Mar 4, 2025 | Equipment & Technology
Ultrasonic Thickness Measurement (UTM-Services) is a non-destructive testing (NDT) technique used to measure the thickness of materials such as metal, composites, and plastics. It utilizes high-frequency sound waves to determine the internal structure and integrity of an object without causing any damage.
How It Works
- Probe Contact – A transducer sends ultrasonic waves into the material.
- Wave Reflection – The waves travel through the material and reflect back from the opposite surface.
- Time Measurement – The time taken for the waves to return is analyzed to calculate the thickness.
- Data Interpretation – The thickness readings are displayed on a digital gauge or stored for further analysis.
Applications
- Industrial Inspection – Used in pipelines, pressure vessels, and storage tanks.
- Marine & Offshore – Checks corrosion and material loss in ship hulls and offshore structures.
- Aerospace – Ensures the structural integrity of aircraft components.
- Manufacturing & Quality Control – Verifies material specifications in production processes.
Advantages of UTM Services
✔ Non-destructive and does not require cutting or damaging the material.
✔ Highly accurate and reliable measurements.
✔ Quick and cost-effective solution for corrosion monitoring.
✔ Can be used on both accessible and hard-to-reach areas.
Benefits of Ultrasonic Thickness Measurement (UTM) on Vessels
Ultrasonic Thickness Measurement (UTM) is a crucial inspection method for vessels, including ships, storage tanks, and pressure vessels. It helps ensure safety, regulatory compliance, and operational efficiency.
6 Benefits of Ultrasonic Thickness Measurement (UTM) on Vessels
1. Corrosion & Erosion Monitoring
- Detects material loss due to corrosion, pitting, or erosion inside the vessel.
- Helps predict maintenance schedules before structural integrity is compromised.
2. Safety & Structural Integrity
- Prevents catastrophic failures by identifying weak spots in the vessel structure.
- Ensures leak prevention, avoiding hazardous spills or explosions.
3. Compliance with Regulations
- Meets industry standards such as ABS, DNV, Lloyd’s Register, ASME, API, and IMO requirements.
- Essential for classification surveys and vessel certification.
4. Non-Destructive & Cost-Effective
- No need to cut or damage the vessel structure.
- Reduces downtime compared to destructive testing methods.
- Minimizes repair costs by addressing issues early.
5. Works in Hard-to-Reach Areas
- Can be used on curved surfaces, tight spaces, and underwater sections.
- Portable equipment allows for on-site inspections without removing components.
6. Data Logging & Trend Analysis
- Provides historical data tracking for long-term corrosion monitoring.
- Helps in predictive maintenance and life cycle assessment of the vessel.
Would you like this tailored for a specific type of vessel (e.g., ships, pressure vessels, offshore platforms)?
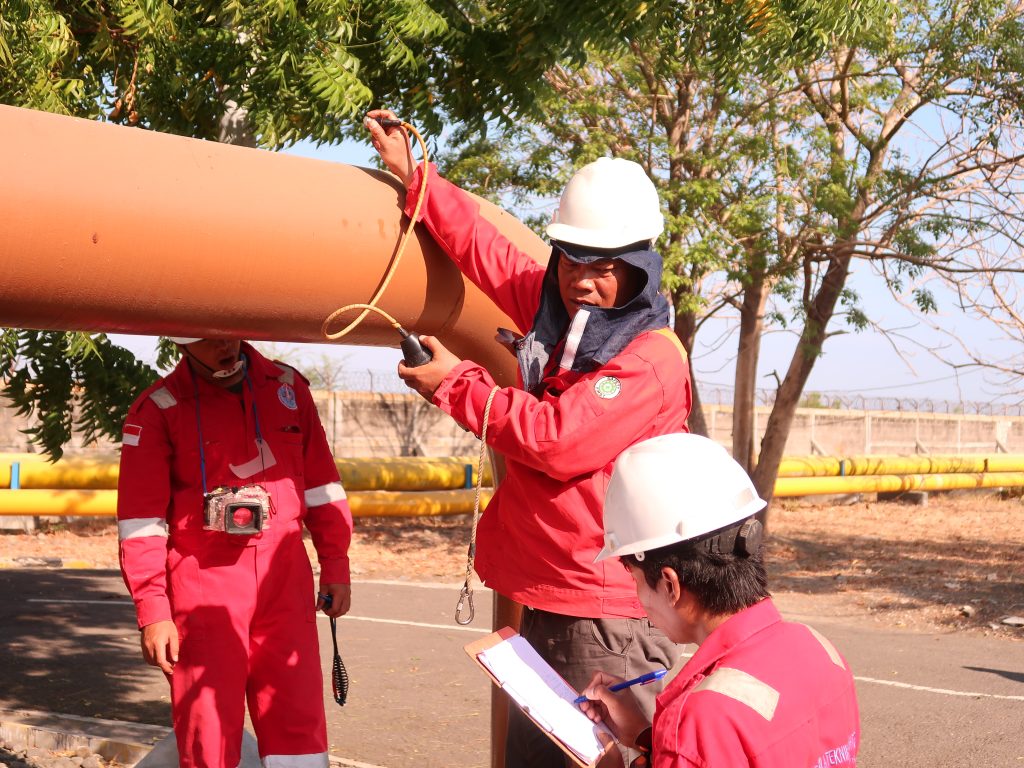